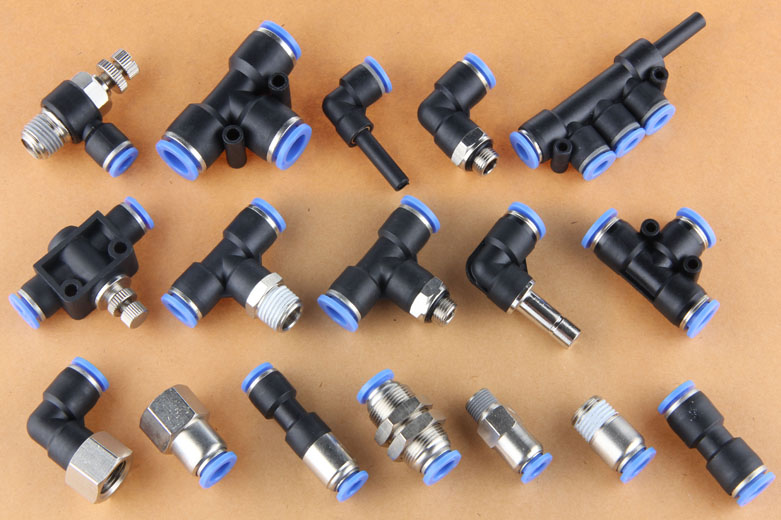
Pneumatic fittings are parts used to connect sections of pipe, tube, and hose in pneumatic (pressurized gas) systems. Compared to hydraulic fittings, pneumatic fittings are typically characterized by tighter seals and lower pressure requirements. They are frequently used in pneumatic logic control systems and instrumentation. Pneumatic tube fittings create connections and filter air in pneumatic systems. Pneumatic inline and tee filters remove unwanted particles from airflow.
It is important to distinguish what type of vessels are being connected in the system to determine what fittings are appropriate.
Commerce Hose & Industrial Products are proud to offer pneumatic tubing and fittings from both Dixon and ATP.
Types of Pneumatic Tubing
- Hoses are flexible vessels that are constructed of multiple layers of different materials. Fittings for hoses are often not permanent, since the hose itself is often replaced in time due to wear.
- Pipes are rigid vessels constructed of one solid material. Generally, pipes are defined by their inner diameter dimension.
- Tubes are fairly rigid vessels constructed of one solid material. Generally, tubes are defined by their outside diameter dimension.
Types of Connections
Pneumatic fittings are attached via a number of different connection methods, each with its own conveniences and advantages.
Ball and Sleeve Fittings
Ball and sleeve fittings connect an outer sleeve to an inner-ball fitting. The sleeve retracts to connect and disconnect the two ends of the fitting. Some ball and sleeve fittings function as push-to-connect fittings which are convenient for applications requiring frequent disconnection and re-connection of the hose section.
Compression Fittings
- Standard compression fittings use metal gaskets, rings, or ferrules which form a seal on the vessel through compression. The compression is typically made by tightening a nut onto the fitting over the piping and ferrule, compressing and securing the vessel inside. Standard compression fittings do not require tools to assemble, making them convenient for quick field installations.
- Bite-type fittings are compressive fittings with a sharpened ferrules that “bites” the vessel when compressed and provides the seal. Bite-type fittings, like standard compressive fittings, require no special tools to assemble, but provide a stronger, higher pressure connection.
- Mechanical grip fittings are two-ferrule assemblies. The back ferrule grips the vessel while pressing up against the front ferrule, which spring-loads the front ferrule and creates a seal between the piping and fitting
body. These fittings can be reassembled multiple times without damaging components or piping. They have good resistance to mechanical vibration. - Flare fittings consist of a body with a flared or coned end. Special flaring tools are used to install the vessel inside the flared end, providing a deep seal. Flare fittings can handle higher pressures and a wider range of operating parameters than standard compression fittings.
Crimp Fittings
Crimp fittings involve placing hose over a tubular end and crimping against it with a sleeve, ring, or crimp socket. These fittings typically require crimping tools or machines to make the connections.
End Fittings
End fittings provide specific surfaces for connecting vessels in pneumatic systems.
- Clamp ends are fittings which allow hoses or tubes to be clamped over the part.
- Plain ends are fittings with surfaces which allow pipes or tubes to be connected by adhesive, solder, welding, or other permanent means.
Push-to-Connect
Push-to-connect fittings have ends that are designed to accept tubing by pushing it into the end. These fittings typically disconnect via some type
of collar retraction. These connections are convenient for sections of the system requiring frequent disconnection and re-connection.
Threaded Fittings
Threaded fittings have screw threads (built-in grooves) on their inner (female) or outer (male) surfaces designed to accept connections with matching threads. Threads which provide a simple connection but no guaranteed seal are called straight threads. Tapered threads are designed to provide a tight seal which is important for pneumatic applications. These precise threads create a “dry fit”, meaning they seal without the need for an additional sealant, which is important in applications where sealant addition could cause contamination or corrosion.